Countersinking, Counterboring, and Spotfacing
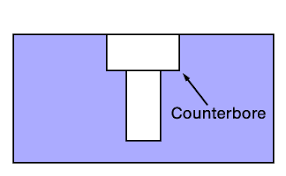

Countersinking, counterboring and spotfacing are machine operations that modify the entrance of an existing hole, usually for seating a screw or bolt. These operations are performed on machines like a drill press, engine lathe, or milling machine. Each of the operations, although similar, employ different cutting tools for the different applications. Countersinks, counterbores, and spotfacers are manufactured in carbon steel, high-speed steel or carbide . These cutters perform best when they are lubricated and operated at 1/4 the calculated RPM. Chattering must be avoided. Chattering is usually caused by excessive speed, improper feed or non-rigid setup.
Countersinking

Countersinking is the operation of producing a taper or cone shape surface at the entrance of a hole for the purpose of having the head of a flat head screw, aviation rivet or other similar fastener sit flush or below a surface. This cone shape is machined with a countersink.
Countersinks are available as a single flute or multi flute. A variety of sizes and included angles of: 60°, 82°, 90°, 100°,110°, and 120° are available. Drawing specifications will determine the angle required. Micrometer stops (left) are available for controlling depth of cut.
Counterboring

Counterboring is the process of enlarging the entrance of a hole with a counterbore, or other similar tool to a specified diameter and depth. Counterbores (below) provide a square shoulder so that a cap screw or bolt head may sit flush or below a surface. Counterbores are available in a variety of sizes and styles. Counterbores may have either a solid or interchangeable pilot to help guide it straight and concentric to the hole. They are held by the shank and are available with straight or Morse taper shanks.
Counterbores have two, three, or four lips or cutting edges known as flutes. Straight flutes are used for brass, spiral flutes are used for most other materials.
Care must be taken on providing solid setups and that proper speeds and feeds are selected for the material being machined. Lubrication will be called for most materials.
Spotfacing

Spotfacing provides a seat or flat surface at the entrance and surrounding area of a hole. This flat surface allows the bottom of a cap screw
or bolt to seat squarely with the material even if the clearance hole
is not normal
to the surrounding material. Spotfacing is commonly done on castings
where irregular surfaces are found. Spotfacing may be performed on a drill press
with a counterbore of suitable size for the operation. A proper

size pilot must be used whenever this is done on the drill press. Spotfacing, when machined on a mill, a center cutting end mill may be the tool of choice. Spotfacing on the lathe is commonly done with a facing tool or form tool.
When drilling on a curved or angular surface, spotfacing is performed before the drilling operation. This process will help the drill start in the proper location and to follow-in straight; in this case, the operator will setup a milling machine with a center cutting end mill (left). The diameter of the end mill should not be smaller that the diameter of the drill. A circular face will then be machined in the proper spot before producing the hole.
0 σχόλια:
Post a Comment